Useful Navi Article Detail Page
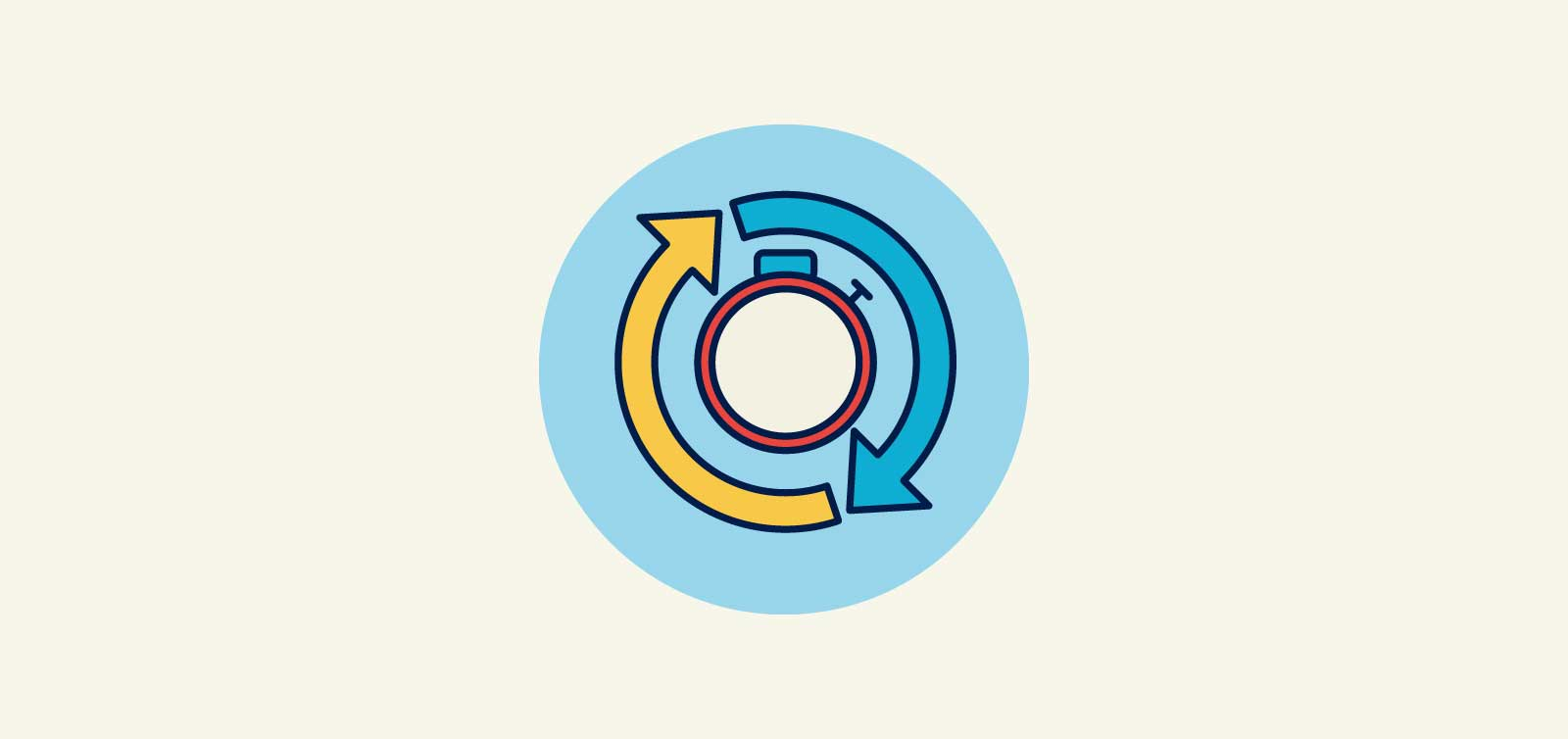
Production efficiency in the manufacturing industry is an essential element for maintaining a company's competitiveness and securing an advantage in the market. "Cycle time" is an important indicator for measuring productivity, and shortening it not only improves production efficiency but also leads to cost reduction and reduced environmental impact. In this article, we will explain the basics of cycle time in machine tools and introduce specific methods for shortening it.
What is the cycle time of a machine tool?
Cycle time refers to the net time taken to make one product. For example, if a machine tool manufactures 30
products in 60 minutes, the cycle time is 2 minutes (=60 minutes ÷ 30 products). Cycle time is closely
related to factors such as product quality, productivity, and cost. Reducing cycle time not only improves
production efficiency, but also leads to various cost reductions such as energy consumption and labor costs. In
addition, terms similar to cycle time include "takt time" and "lead time." Takt time refers to the "time
required to manufacture one product" and is calculated by "operating time ÷ required production
quantity."
While cycle time is an indicator of production capacity, takt time is characterized by being based on the number
of orders from customers and the number of products that can be sold. In addition, lead time is a term that
means "the time it takes from ordering to delivery."
The path to shorter cycle times?
When considering cycle time reduction, it is important to divide cycle time into "cutting time" and
"non-cutting time".
Cutting time: Time when the machine tool is cutting
Non-cutting time: Time when the machine tool is not cutting
Cutting time refers to the time when the workpiece is actually being processed, while non-cutting time
refers to the time spent on non-processing such as part replacement, tool replacement, and machine operation
lag. When working on cycle time reduction, it is important to approach both of these.
In addition, it is essential to understand "how much time is being spent on which part" in the current
process. It is also effective to take a video of the actual work and check whether there is any waste. There
are many approaches to reducing cycle time, such as adjusting cutting conditions, reviewing the work
environment, and training and educating operators. Starting with understanding the current situation,
formulating and implementing specific improvement measures, and measuring the effects, this series of steps
is the standard for reducing cycle time.
4 Ways to Reduce Cycle Time
Optimizing cutting conditions
Optimizing cutting conditions is a basic step in shortening cycle time. Adjust the rotation speed and feed rate, and reconsider the settings that are appropriate for each workpiece. In principle, increasing the cutting conditions shortens the cutting time, but on the other hand, the chip wear increases accordingly. This may result in more frequent chip replacements, making it difficult to shorten the cycle time as desired. Therefore, in order to shorten cycle time, it is important to find cutting conditions that are well balanced, taking into account factors such as time and cost.
Reducing idling time
Reducing idling time, which is non-cutting time, also leads to shorter cycle times. For example, consider whether there is any waste, overburdening, or unevenness in the work process, such as changing the placement of workpieces and tools, or doing other work while cutting the workpiece. Thorough implementation of the 5S (sort, set in order, shine, standardize, and discipline) can improve work efficiency and shorten cycle times, so look around the entire workplace to find room for improvement.
Automate your work
In recent years, machine tools have various functions, and machines with advanced automation functions are also appearing. By introducing such machine tools, efficient machining with minimal human intervention is possible. For example, 5-axis machining centers can perform multi-sided machining at once, so cycle times can be significantly shortened. In addition, machining centers equipped with multiple pallets and pallet changers can perform non-stop machining without stopping the machine for pallet changes.
Improving operator skills
It is also very important to improve the skills of operators. If operators can perform efficient work through regular training and education, mistakes and inefficient operations can be reduced. As a result, cycle time will be shortened, so be sure to check whether human factors are a bottleneck.
The quickest way to reduce cycle time is to introduce high-performance machine tools
The improvements in cutting conditions and work processes introduced above are expected to have a certain effect
in shortening cycle time. However, in reality, manufacturers probably think that "they have already improved the
skills of their workers and reviewed their production processes." If you want to drastically shorten cycle time,
the shortest route is to introduce new machine tools. This is not an initiative that can be implemented
immediately because it requires a large investment, but technological progress has been remarkable in recent
years, and the latest machine tools have evolved to process parts with overwhelming speed and precision compared
to conventional ones.
For example, there are cases where companies that have newly introduced Brother Industries' machining center
"SPEEDIO" have been able to "reduce cycle time by more than 20%" and "reduce processing time by 40%."
In addition, SPEEDIO has excellent environmental performance, so you can also expect a reduction in electricity
consumption. If your machine tools are aging or you are using general-purpose machine tools operated by workers,
introducing new machine tools should provide various benefits.
Reduce financial burden by taking advantage of subsidies for introducing machine tools
Introducing new machine tools can cost anywhere from several million to several tens of millions of yen. This can be a huge burden for a typical small or medium-sized business, so you should consider whether you can take advantage of subsidies or grants. The following are some of the systems you can use when introducing new machine tools.
Manufacturing Subsidy | A system that provides subsidies for capital investment aimed at developing new products and services, improving production processes, etc. | Top page | Official website of the manufacturing subsidy program Manufacturing subsidy general site |
---|---|---|
Small Business Sustainability Subsidy |
A system that subsidizes part of the expenses incurred in expanding sales channels and improving productivity | Small Business Sustainability Subsidy (General Type)[New Window] |
Energy-saving equipment investment interest subsidy |
A system that subsidizes part of the interest on loans from financial institutions for capital investments that lead to energy conservation. | SII: Environmental Co-Creation Initiative (General Incorporated Association) | Business Top (FY2023 Energy Saving Equipment Investment Interest Subsidy) |
Business restructuring subsidy |
A system to support small and medium-sized enterprises in their efforts to restructure their businesses and increase added value in order to encourage them to adapt to the changes in the economy and society brought about by the COVID-19 pandemic. | Top Page | Business Restructuring Subsidy[New Window] |
Subsidy for Energy Saving Investment Promotion Support Project | A system that subsidizes part of the cost of installing high-performance energy-saving equipment with the aim of reducing fuel and power consumption. | SII: Environmental Co-Creation Initiative (General Incorporated Association) | Project Top (FY2022 Supplementary Budget Energy Saving Investment Promotion Support Project) |
High-performance machine tools require initial costs, but these subsidies and grants can significantly reduce that burden. Companies considering introducing them should check the latest information on the details of each system and how to apply.
Reducing cycle time is an important indicator that directly relates to productivity
Cycle time is an important indicator for measuring productivity. By optimizing cutting conditions, reducing idling time, automating tasks, etc., cycle time can be shortened, which will improve production efficiency and reduce costs. In addition, machine tool technology has evolved remarkably in recent years, and cycle time can be significantly shortened by introducing new machine tools. Although an initial investment is required, it is possible to reduce the burden of introduction by taking advantage of subsidies and grants from the national and local governments. Identify the issues your company faces and take appropriate measures to reduce cycle time.
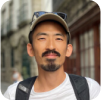
Text: Yuki Kobayashi

Edited by EasyGo Inc.
Related Articles
Support Information
