SPEEDIO U500Xd1
Universal Compact Machining Center
- Travels (mm): X: 500 Y: 400 Z: 300
- Max. spindle speed (min-1): 10,000/ (Optional) 16,000
- Tool storage capacity(pcs.): 14/ 21/ 28
Select variants: U500Xd1-5AX
Equipped with a newly developed tilting rotary table with a maximum jig area of 500 mm in diameter. Combination with a 28-tool magazine enables multi-face machining that breaks the conventional concept of #30 machines.
Information
Overview
One-clamp machining encourages process integration.
Max. loading capacity : 100kg
* A 14-tool magazine or a 21-tool magazine can be also selected.
Max. tool weight : 4kg*
* Parameter setting needs to be changed.
The Y-axis travel range has been shifted from the center of the tilt axis to secure sufficient machining area when the tilt axis is at 90 degrees. (Y-axis travel when A-axis is at 90 degrees: 270 mm)
28-tool magazine
Chip - Chip: 1.3 s
Tool - Tool: 0.7 s
Equipped with a highly efficient spindle motor that demonstrates sufficient torque from the low- to high-speed range.
Achieves highly efficient machining in various industries, from automobile to general machinery, medical, and aircraft industries.
Tool center point control has been added to support simultaneous five-axis machining.*
*Available only for the U500Xd1-5AX.
10,000 min-1 (standard)
Max. torque : 40Nm
Max. output : 18.9kW
A-axis clamp torque* : 810Nm
C-axis clamp torque* : 560Nm
Tool center point control comes with a variety of functions. This achieves high-speed and highly accurate simultaneous 5-axis machining in combination with a backlash-free tilting rotary table.
Tool center point control
Equipped with tool center point control where machining is performed by changing the tool direction relative to the workpiece.
Optimal acceleration by look-ahead up to 1,000 blocks achieves simultaneous 5-axis machining.
NC functions related to simultaneous 5-axis machining*
Tool center point control (look-ahead 1,000 blocks),
submicron command, feature coordinates setting, memory capacity (3 Gbytes)
*All functions are standard on the U500Xd1-5AX
Specifications
Product Specification
U500Xd1
Max. spindle speed
10,000/ (Optional) 16,000
Travels
X: 500 Y: 400 Z: 300 A(deg.): -30 to 120 C(deg.):360
Tool storage capacity
14/ 21/ 28
Rapid traverse rate (XYZ-area)
50 x 50 x 56
Indexing speed (A,C)
A:50 C:75
Required Floor Space
1,560 x 2,026
BT dual contact spindle(BIG-PLUS)
Optional
Coolant Through Spindle(CTS)
Optional
Item | U500Xd1 / U500Xd1 RD *8 | U500Xd1-5AX / U500Xd1-5AX RD *8 | ||
---|---|---|---|---|
CNC Unit | CNC-D00 | CNC-D00v (DB) | ||
Travels | X axis [mm (inch)] | 500 (19.7) | ||
Y axis [mm (inch)] | 400 (15.7) | |||
Z axis [mm (inch)] | 300 (11.8) | |||
A axis [deg.] | 120 to -30 | |||
C axis [deg.] | 360 | |||
Distance between table top and spindle nose end [mm (inch)] | 145 - 445 (5.7 - 17.5) | |||
Table | Work area size [mm (inch)] | ø260 (ø10.2) | ||
Max.loading capacity (uniform load) [kg (lbs)] |
100 (220) | |||
Max. table load inertia | 1.8 (6151) [2.6 (8885) *9] | |||
Spindle | Spindle speed [min-1] |
10,000min-1 specifications : 1 - 10,000 16,000min-1 specifications(Optional) : 1 - 16,000 |
||
Speed during tapping [min-1] | MAX. 6,000 | |||
Tapered hole | 7/24 tapered No.30 | |||
BT dual contact system (BIG-PLUS) |
Optional | |||
Coolant Through Spindle (CTS) | Optional | |||
Feed rate | Rapid traverse rate (XYZ-area) [m/min (inch/min)] |
50 x 50 x 56 (1,969 x 1,969 x 2,205) | ||
Cutting feed rate [mm/min (inch/min)] |
X, Y, Z axis: 1 - 30,000 (0.04 - 1,181) *7 | |||
Indexing feedrate (A and C) | A axis: 50, C axis: 75 (60) *9 | |||
ATC unit | Tool shank type | MAS-BT30 | ||
Pull stud type*4 | MAS-P30T-2 | |||
Tool storage capacity [pcs.] | 14/21/28 | |||
Max.tool length [mm (inch)] | 250 (9.8) | |||
Max.tool diameter [mm (inch)] | 110 (4.3) | |||
Max.tool weight [kg (lbs)]*1 | 3.0 (6.6) [4.0 (8.8) *10] / tool, |
|||
Tool selection method | Random shortcut method | |||
Tool change time *5 | Tool To Tool [sec.] | 0.6 / 0.7 (14 or 21 tools / 28 tools) | ||
Chip To Chip [sec.] | 1.2 / 1.3 (14 or 21 tools / 28 tools) | |||
Electric motor | Main spindle motor (10 min/continuous)[kW] *2 |
10,000min-1 specifications : 10.1/7.1
16,000min-1 specifications(Optional) : 7.4/5.1 |
||
Axis feed motor [kW] | XY axis: 1.0, Z axis: 2.0, A axis: 0.9, C axis: 0.55 | |||
Power source | Power supply | AC 200 to 230 V±10%, 3-phase, 50/60Hz±2% | ||
Power capacity (continuous) [kVA] | 10,000min-1 specifications : 9.5
16,000min-1 specifications(Optional) : 9.5 |
|||
Air supply | Regular air pressure [MPa] | 0.4 - 0.6(recommended value : 0.5MPa)*6 | ||
Required flow [L/min] | 55L/min | |||
Machine dimensions | Height [mm (inch)] | 2,748 (108.2) | ||
Required floor space*11 [with control unit door open] [mm (inch)] |
1.560 x 2,026 [2,864] (61.4 x 79.8 [112.8]) | |||
Weight [kg (lbs)] | 2,650 (5,843) | |||
Accuracy*3 | Accuracy of bidirectional axis positioning (ISO230-2:1988) [mm (inch)] |
X, Y, Z axis: 0.006~0.020 (0.00024~0.00079) /A, C axis: 28 sec or less | ||
Repeatability of bidirectional axis positioning (ISO230-2:2014) [mm (inch)] |
X, Y, Z axis: Less than 0.004 (0.00016) /A, C axis: 16 sec or less | |||
Standard accessories | Instruction Manual (DVD 1 set), leveling bolts (4 pcs.), leveling plate (4 pcs.) |
- *1 Actual tool weight differs depending on the configuration and center of gravity. The figures shown here are for reference only.
- *2 Spindle motor output differs depending on the spindle speed.
- *3 Measured in compliance with ISO standards and Brother standards. Please contact your local distributor for details.
- *4 Brother specifications apply to the pull studs for CTS.
- *5 Measured in compliance with JIS B6336-9 and MAS011-1987.
- *6 Regular air pressure varies depending on the machine specifications, machining program details, or use of peripheral equipment. Set the pressure higher than the recommend value.
- *7 When using high accuracy mode B.
- *8 The machine needs to be equipped with a relocation detection device depending on the destination. Machines equipped with a relocation detection device come with "RD" at the end of the model name.
- *9 When using high inertia mode. Parameter setting needs to be changed.
- *10 Parameter setting needs to be changed. (Tool indexing time is changed.)
- *11 The value does not include the coolant tank.
CNC model | 《U500Xd1》 | CNC-D00 |
---|---|---|
《U500Xd1-5AX》 | CNC-D00v (DB) | |
Control axes | 5 axes (X, Y, Z, A, C) | |
Simultaneously controlled axes 《U500Xd1》 |
Positioning | 5 axes (X, Y, Z, A, C) |
Interpolation |
Linear : 4 axes (X, Y, Z, one additional axis)
Circular : 2 axes Helical/Conical : 3 axes (X, Y, Z) |
|
Simultaneously controlled axes 《U500Xd1-5AX》 |
Positioning | 5 axes (X, Y, Z, A, C) |
Interpolation |
Linear : 5 axes (X, Y, Z, 2 additional axes)
Circular : 2 axes Helical/Conical : 4 axes (3 linear axes + 1 additional axis, 2 linear axes + 2 additional axes) |
|
Least input increment | 0.001mm、0.0001inch、0.001 deg. | |
Max.programmable dimension | ±999999.999mm、±99999.9999inch | |
Display | 15-inch color LCD touch display | |
Memory capacity *Total capacity of program and data bank |
《U500Xd1》 | 500 Mbytes, 3 Gbytes (optional) |
《U500Xd1-5AX》 | 3 Gbytes | |
External communication | USB memory interface, Ethernet, RS232C (optional) | |
No.of registrable programs | 4,000 (Total capacity of program and data bank) | |
Program format | NC language, conversation (changed by parameter) Conversation from conversation program to NC language program available |
- * “Control axes” and “Simultaneously controlled axes” indicate the maximum number of axes, which will differ depending on the destination country and the machine specifications.
- * Ethernet is a trademark or registered trademark of XEROX in the United States.
Operation | Dry run Machine lock Program restart Rapid traverse override Cutting feed override Background editing Screen shot Operation level External input signal key Shortcut keys
|
|
---|---|---|
Programming | Absolute / Incremental Inch / Metric Coordinate system setting Corner C / Corner R Rotational transformation Synchronized tap Subprogram Graphic display |
|
Measurement | Automatic workpiece measurement *1 Tool length measurement |
|
High speed and high accuracy | Machining parameter adjustment High-accuracy mode AIII High-accuracy mode BI (look-ahead 160 blocks) Backlash compensation Tool center point control *3 (Look-ahead 1,000 blocks)
|
|
Monitoring | Machining load monitoring ATC monitoring Overload prediction Waveform display / Waveform output to memory card Heat expansion compensation system ll (X, Y, and Z axes) Production performance display Tool life / Spare tool |
|
Maintenance | Tap return function Status log Alarm log Operation log Maintenance notice Motor insulation resistance measurement Tool washing filter with filter clogging detection Battery-free encoder Breake load test |
|
Automatic / Network | Computer remote OPC UA Auto notification Built-in PLC (LD/ST/FBD)
|
|
Energy saving | Automatic power off Standby mode Automatic coolant off Automatic work light off Chip shower off delay |
|
Support apps | Adjust machine parameters ATC tool Tool life Waveform display Production performance Power consumption Recovery support Inspection PLC |
|
Accessories | File viewer Notebook Calculator Register shortcut Display off |
|
Functions limited to NC language | Menu programming Local coordinate system Expanded workpiece coordinate system One-way positioning Inverse time feed Programmable data input Tool length compensation Cutter compensation Scaling Mirror image External sub program call Macro Operation in tape mode Multiple skip function
|
|
Functions limited to conversation | Operation program Schedule program Automatic tool selection Automatic cutting condition setting Automatic tool length compensation setting Automatic cutter compensation setting Automatic calculation of unknown number input Machining order control |
- *1 Measuring instrument needs to be prepared by users.
- *2 When the submicron command is used, changing to the conversation program is disabled.
- *3 Available only for the U500Xd1-5AX.
- *4 Standard on the U500Xd1-5AX.
Example
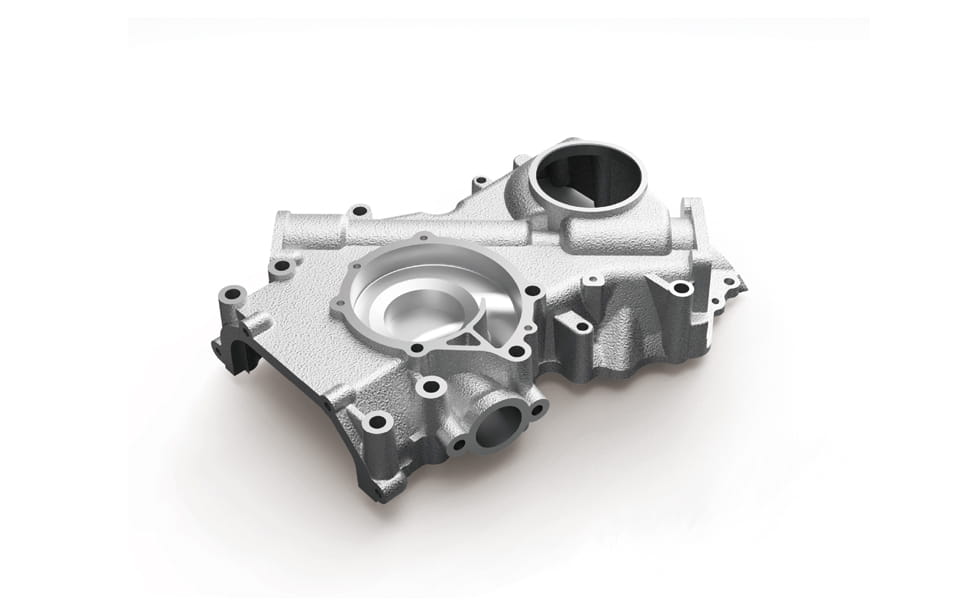
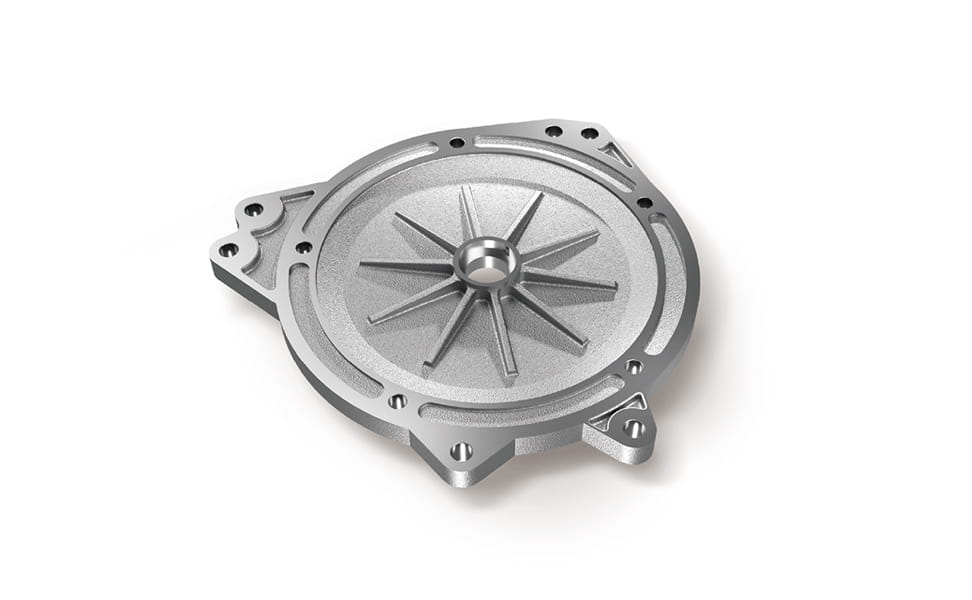
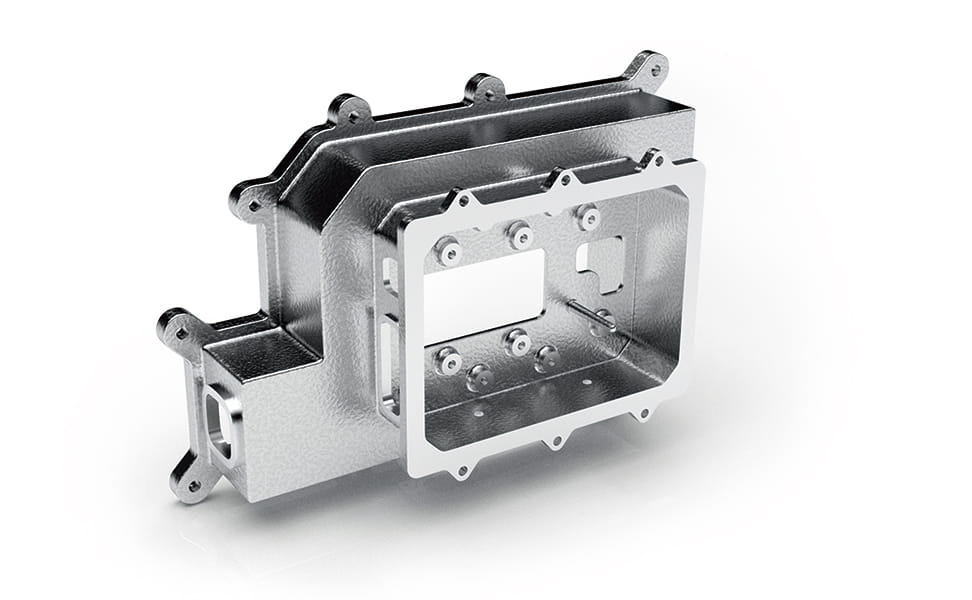
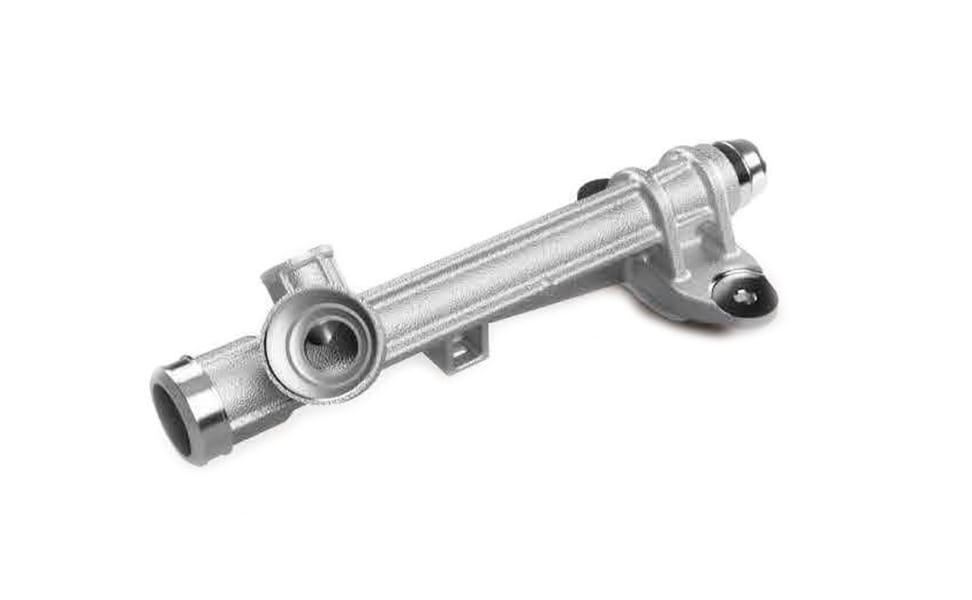
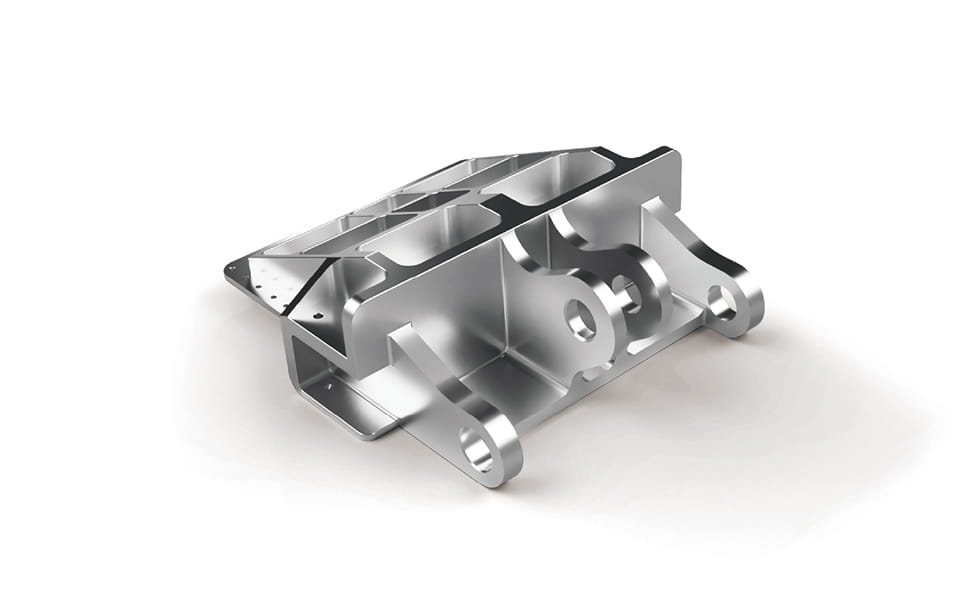
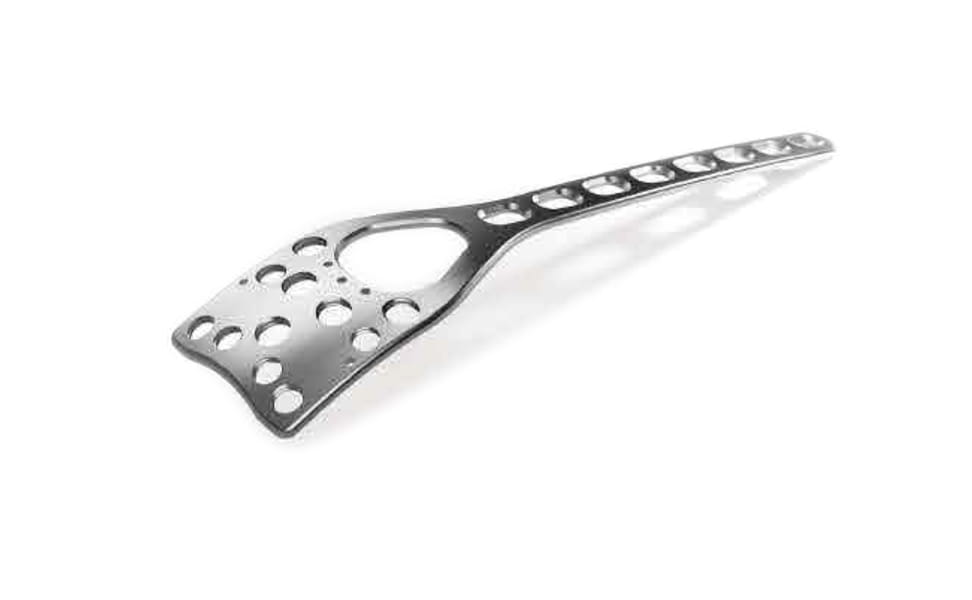