SPEEDIO S500Xd2-5AX
Compact Machining Center
- Travels (mm): X: 500 Y: 450 Z: 300/ (Optional)380
- Max. spindle speed (min-1): 12,000/ (Optional) 16,000/ (Optional) 27,000/ (Optional) 10,000 high-torque
- Tool storage capacity(pcs.): 14/ 21/ 28
Select variant: S700Xd2-5AX 100T
Enlarged machining area and using a 28-tool magazine expand target workpieces andpromote process integration.
Advanced CNC-D00 controller improves environmental performance and productivity.
Information
Overview
Increased travels of Y/Z axes, bigger table, and using a 28-tool magazine expand the range of application for process integration, such as for multi-face machining, and variable-product variable-volume production.
Together with the extensive range of specifications, the machine responds to a wide variety of machining.
Increased Y-axis travel expands the range of target workpieces.
Y-axis travel
400mm (Previous model) → 450mm
Bigger table expands the range of jig selection.
S300/S500Xd2 600 X 400* → 600 X 450mm
S700Xd2 800 X 400* → 800 X 450mm
* Values of previous modelIn addition to the standard 300 mm Z-axis travel, the 380 mm Z-axis travel can be selected.
The Z-axis travel and the distance between the table top and spindle nose end have been increased to secure ample machining area in the Z-axis direction and improve tool accessibility.
* The Z-axis 380 mm spec. cannot be selected for the S300Xd2.
Z-axis travel
300mm (standard) 380mm (optional)
Distance between table top and spindle nose end
180 - 480mm (standard) 150 - 530mm (optional)
28-tool magazine *
This is a compact drum type magazine that achieves high-speed tool change. The magazine can be selected from a 14-tool, 21-tool, or 28-tool magazine. The maximum tool weight is 4 kg.
* The 28-tool magazine cannot be selected for the S300Xd2.
28-tool magazine
Max. tool diameter 110mm
Max. tool weight 4kg
Max. total tool weight 35kg
Tool-Tool 0.7s
Optimized control by the CNC-D00 controller eliminates waste to the utmost limit in every operation during machining. This maximizes the performance of the highly reliable machine and ensures high productivity.
Non-stop ATC
High-speed tool change has been achieved by faster and optimized spindle start/stop,
Z-axis up/down, and magazine operation. Tools up to 3 kg can be changed in the shortest time. Tools up to 4 kg can also be changed with minimal increase in time.
14/21 tools (Standard tools) Tool-Tool: 0.6s / Chip-Chip*: 1.2s
28 tools (Standard tools) Tool-Tool: 0.7s / Chip-Chip*: 1.3s
28 tools (Heavy tools) Tool-Tool: 0.8s / Chip-Chip*: 1.4s
* Values for Z-axis 300 mm spec.
Magazine load conditions estimate
Estimates the inertia and unbalanced load of the tool loaded in the magazine, and sets the optimum value for the acceleration of the magazine axis. In addition, automatically updates the value to the estimated optimum acceleration, even during programmed operation.
High acceleration/deceleration spindle
As the Z-axis moves frequently, the highest acceleration in its class has been achieved, contributing to reduction in cycle time.
Z-axis acceleration Max. 2.2G
Improved automatic door opening/closing speed
The automatic door opening/closing speed has been improved, enabling significant reduction in setup time.
Automatic door opening/closing time 20% less
Simultaneous operation
Wasted time has been reduced by simultaneously performing tool change and positioning X/Y and additional axes.
Optimal X/Y axes acceleration setting
Load weight Is estimated by moving the table to set the optimal acceleration for the X/Y axes.
No warmup support function
Equipped with an original measurement processing function that reduces the number of actual measurements by a touch probe according to the size of displacement.
This eliminates the need for warmup operation, minimizing effects on productivity to achieve highly accurate machining.
A variety of spindles are available to meet a wide range of industries, from automobile to semiconductor, precision parts, and IT equipment industries.
The NC unit achieves high-speed and highly accurate three-dimensional machining or simultaneous 5-axis machining *.
* Simultaneous 5-axis machining is available only on the S300/500/700Xd2-5AX.
Newly developed and highly efficient 12,000 min-1 spindle motor
The standard motor specifications have been upgraded from the previous 10,000 min-1 to a newly developed 12,000 min-1. As spindle torque is maintained in the medium- and high-speed range, this achieves further reduction in machining time when performing highly efficient machining of aluminum or steel at high speed.
High-torque spec. (optional)
Max. torque 92N・m
Max. output 26.2kW
12,000 min-1 spec. (standard)
Max. torque 40N・m
Max. output 18.9kW
Improved spindle rigidity
For 10,000 min-1 high-torque specifications (optional), the spindle bearing diameter has been enlarged to enhance rigidity.
The machine demonstrates its capabilities in a wide variety of machining applications, including heavy-duty machining of steel.
Spindle clamp force
Improved by 15%
Spindle bearing diameter (high-torque spec.)
Larger by 10%
Side cutting
Enhanced spindle rigidity improves the wall squareness during side cutting and increases the cutting amount.
Wall squareness
10% better than previous model
Simultaneous 5-axis machining
Equipped with a variety of functions, including tool center point control and submicron command, to achieve high-speed and highly accurate simultaneous 5-axis machining.
* Changing to the conversation language is not possible for the simultaneous 5-axis specifications (5AX).
Tool center point control
Equipped with tool center point control where machining is performed by changing the tool direction relative to the workpiece. Optimal acceleration/deceleration by look-ahead up to 1,000 blocks achieves simultaneous 5-axis machining.
Processing speed of minute line segments
The CPU capacity has been greatly increased to enhance the processing speed of minute line segments by four times the previous controller. This enables high-speed processing of CAM data with small tolerance.
Maintenance functions have been enhanced to prevent machine failure, with measures for chips taken to reduce machining defects.
Thorough avoidance of machine stoppage maintains high productivity at production sites.
Tool cleaning system (optional)
The number of discharge holes and the angle of these holes have been optimized to significantly increase the discharge flowrate. This has resulted in a threefold ncrease in cleaning capacity, compared to the previous model.
When CTS is selected, coolant for tool cleaning is discharged from the CTS pump, consuming less air than air-assisted tool cleaning.
* When CTS is not selected, air-assisted tool cleaning is used
The new 100-tool magazine, featuring the largest storage capacity in the SPEEDIO series, has been developed. *1
Brother’s original mechanism achieves space saving and high productivity.
*1. Mounted only on the S700Xd2-100T. Conversation language not available on the S700Xd2-100T.
Newly developed 100-tool magazine
A tool stocker that can store 36 tools is installed on the right and left sides of the 28-tool turret magazine, enabling storage of 100 tools, the largest capacity in the SPEEDIO series.
Brother’s original tool handling mechanism achieves stable tool change.
100-tool magazine spec.
Turret magazine : 28 tools
Tool stocker (left/right) : 36 tools each
Total storage capacity : 100 tools
The stocker shutter separates the tool stocker from the machining chamber, minimizing the effect of chips on tools.
Space-saving design High productivity
Tool stockers are installed inside the machine to save space while storing 100 tools.
*1. Does not include coolant tank and chip conveyor
*2. Compared to BT40 vertical MC with equivalent tool storage capacity
High productivity
If the number of tools used in machining is 28 or less, high speed tool change is possible using only the turret magazine, leading to high productivity.
Even when using tools in the tool stocker, handling is possible within approximately 5 seconds (1 tool).
In addition, all tools in the turret magazine can be easily changed, reducing setup time.
Turret magazine tool change time
Tool to Tool : 0.7s
Chip to Chip : 1.4s
Tool stocker handling time *3
Shortest (1 tool) : Approx. 5s
All tool change (28 tools) : Approx. 140s
*3. Handling time varies depending on the tool attachment position.
Tool stocker management function
A function for managing the 100-tool magazine has been added to the ATC tool app.
Tool change operation is intuitive, and tools to be used in the machining program can be moved from the tool stocker to the turret magazine in a batch.
In addition, data of tools in the tool stocker can be easily changed.
100-tool magazine + Ample jig area
For high-mix small-lot workpieces, the 100-tool magazine eliminates the need for frequent tool changes, and the ample jig area enables multiple jigs to be mounted.
These features significantly improve the efficiency of high-mix small-lot production.
Making automation and manpower saving easier
Side shutter (optional)
Assuming loading/unloading of workpieces from the side by robots, a side shutter has been prepared to make automation easier.
* A safety fence is required. Cannot be selected for the S300Xd2.
Chip conveyor (optional)
Two types of chip conveyors are available: scraper type and hinge + scraper type.
* Chip conveyors can only be selected for the S700Xd2-100T.
Specifications
Product Specification
S500Xd2-5AX
Max. spindle speed
12,000/ (Optional) 16,000/ (Optional) 27,000/ (Optional) 10,000 high-torque
Travels
X: 500 (19.7) Y: 450 (17.7) Z: 300 (11.8) / (Optional)380 (15.0)
Tool storage capacity
14/ 21/ 28
Rapid traverse rate (XYZ-area)
50 x 50 x 56 (1,969 x 1,969 x 2,205)
Required Floor Space
1.560 x 2,081 (61.4 × 81.9)
BT dual contact spindle(BIG-PLUS)
Optional
Coolant Through Spindle(CTS)
Optional
Item | S300Xd2 S300Xd2 RD *9 S300Xd2-5AX S300Xd2-5AX RD *9 |
S500Xd2 S500Xd2 RD *9 S500Xd2-5AX S500Xd2-5AX RD *9 |
S700Xd2 S700Xd2 RD *9 S700Xd2-5AX S700Xd2-5AX RD *9 |
S700Xd2-100T S700Xd2-100T RD *9 S700Xd2-5AX/100T S700Xd2-5AX/100T RD *9 |
||||
---|---|---|---|---|---|---|---|---|
CNC Unit | [S300Xd2/S500Xd2/S700Xd2] CNC-D00 [S300Xd2-5AX/S500Xd2-5AX/S700Xd2-5AX] CNC-D00v(DB) |
|||||||
Travels | X axis [mm (inch)] | 300 (11.8) | 500 (19.7) | 700 (27.6) | ||||
Y axis [mm (inch)] | 450 (17.7) | |||||||
Z axis [mm (inch)] | 300 (11.8) | 300 (11.8) | 380 (15.0) | 300 (11.8) | 380 (15.0) | 380 (15.0) | ||
Distance between table top and spindle nose end [mm (inch)] | 180 - 480 (7.1 - 18.9) | 180 - 480 (7.1 - 18.9) |
150 - 530 (5.9 - 20.9) |
180 - 480 (7.1 - 18.9) |
150 - 530 (5.9 - 20.9) |
150 - 530 (5.9 - 20.9) |
||
Table | Work area size [mm (inch)] | 600 × 450 (23.4 × 17.7) | 800 × 450 (31.4 × 17.7) | |||||
Max.loading capacity (uniform load) [kg (lbs)] |
250 [300 *6] (551 [661 *6]) |
250 [400 *6] (551 [881 *6]) |
||||||
Spindle | Spindle speed [min-1] | 12,000min-1 specifications : 1 - 12,000 16,000min-1 specifications(Optional) : 1 - 16,000 10,000min-1 high-torque specifications(Optional) : 1 - 10,000 27,000min-1 specifications(Optional) : 1 - 27,000 (27,000min-1 specifications cannot be selected for Z-axis 380 mm specifications models) |
12,000min-1 specifications : 1 - 12,000 10,000min-1 high-torque specifications(Optional) : 1 - 10,000 |
|||||
Speed during tapping [min-1] | Max. 6,000 (27,000min-1 specifications : Max. 8,000) | Max. 6,000 | ||||||
Tapered hole | 7/24 tapered No.30 | |||||||
BT dual contact system (BIG-PLUS) |
Optional | |||||||
Coolant Through Spindle (CTS) | Optional (CTS cannot be selected for 27,000min-1 specification models) | Optional | ||||||
Feed rate | Rapid traverse rate (XYZ-area) [m/min (inch/min)] |
50 x 50 x 56 (1,969 x 1,969 x 2,205) | ||||||
Cutting feed rate [mm/min (inch/min)] |
X,Y,Z: 1 - 30,000 ( 0.04 - 1,181) *7 | |||||||
ATC unit | Tool shank type | MAS-BT30 | ||||||
Pull stud type*4 | MAS-P30T-2 | |||||||
Tool storage capacity [pcs.] | 14 / 21 | 14 / 21 / 28 | 100 *12 | |||||
Max.tool length [mm (inch)] | 160 (6.3) [21tool] 250 (9.8) [14tool] |
250 (9.8) | ||||||
Max.tool diameter [mm (inch)] | 110 (4.3) | Turret magazine: 110 (4.3), Tool stocker: 60 (2.3) / 110 (4.3) (No adjacent tool) |
||||||
Max.tool weight [kg (lbs)]*1 | 3.0 (6.6) [4.0 (8.8) *10]/tool, |
Turret magazine: 3.0 (6.6) [4.0 (8.8) *10] / tool,(Total tool weight: 35 (77.2)) Tool stocker: 4.0 (8.8) / tool, |
||||||
Tool selection method | Random shortcut method | |||||||
Tool change time *5 | Tool To Tool [sec.] | 0.6 / 0.7 (14 or 21 tools / 28 tools) | 0.7 *13 | |||||
Chip To Chip [sec.] | Z-axis 300 mm specifications : 1.2 / 1.3 (14 or 21 tools / 28 tools) Z-axis 380 mm specifications : 1.3 / 1.4 (14 or 21 tools / 28 tools) |
1.4 *13 | ||||||
Electric motor | Main spindle motor (10 min/continuous)[kW] *2 |
12,000min-1 specifications : 10.1/7.0 16,000min-1 specifications(Optional) : 7.4/5.1 10,000min-1 high-torque specifications(Optional) : 12.8/9.2 27,000min-1 specifications(Optional) : 8.9/6.3 |
12,000min-1 specifications: 10.1/7.0, 10,000min-1 high-torque specifications (optional):12.8/9.2 | |||||
Axis feed motor [kW] | X,Y: 1.0 / Z: 2.0 | |||||||
Power source | Power supply | AC 200 to 230 V±10%, 3-phase, 50/60Hz±2% | ||||||
Power capacity (continuous) [kVA] | 12,000min-1 specifications : 9.5 16,000min-1 specifications(Optional) : 9.5 10,000min-1 high-torque specifications(Optional) : 10.4 27,000min-1 specifications(Optional) : 9.5 |
12,000min-1 specifications : 9.5, 10,000min-1 high-torque specifications(Optional) : 10.4 | ||||||
Air supply | Regular air pressure [MPa] | 0.4 - 0.6(recommended value : 0.5MPa *8) | ||||||
Required flow [L/min] | 40 (27,000min-1 specifications:115) | 40 | ||||||
Machine dimensions | Height [mm (inch)] | Z-axis 300 mm specifications: 2,529 (99.6) Z-axis 380 mm specifications: 2,568 (101.1) |
2,568 (101.1) | |||||
Required floor space *11 [with control unit door open] [mm (inch)] |
1,080 × 2,161 [2,999] (42.5 × 85.1[118.1]) |
1.560 × 2,081 [2,919] (61.4 × 81.9[114.9]) |
2,050 × 2,081 [2,919] (80.7 × 81.9[114.9]) |
2,050 x 2,081 [2,919] (80.7 x 81.9 [114.9]) | ||||
Weight[with BV7-870Ad] [kg (lbs)] |
2,350 (5,181) [2,650(5,843)] |
2,400 (5,292) [2,700(5,953)] |
2,550 (5,622) | 2,700 (5,953) | ||||
Accuracy*3 | Accuracy of bidirectional axis positioning (ISO230-2:1988) [mm (inch)] |
0.006 - 0.020 (0.00024 - 0.00079) | ||||||
Repeatability of bidirectional axis positioning (ISO230-2:2014) [mm (inch)] |
Less than 0.004 (0.00016) | |||||||
Front door | 2doors | |||||||
Standard accessories | Instruction Manual (DVD 1 set), leveling bolts (4 pcs.), leveling plate (4 pcs.) |
- *1 Actual tool weight differs depending on the configuration and center of gravity. The figures shown here are for reference only.
- *2 Spindle motor output differs depending on the spindle speed.
- *3 Measured in compliance with ISO standards and Brother standards. Please contact your local distributor for details.
- *4 Brother specifications apply to the pull studs for CTS.
- *5 Measured in compliance with JIS B6336-9 and MAS011-1987.
- *6 Parameter adjustment is required. (Acceleration adjustment and positioning speed are also changed according to the weight.)
- *7 When using high accuracy mode B.
- *8 Regular air pressure varies depending on the machine specifications, machining program details, or use of peripheral equipment. Set the pressure higher than the recommend value.
- *9 The machine needs to be equipped with a relocation detection device depending on the destination. Machines equipped with a relocation detection device come with “RD” at the end of the model name.
- *10 Parameter setting must be changed. (Tool indexing time will change.) Max. tool weight 4.0 kg cannot be available for the 27,000 min-1 specifications.
- *11 The value does not include the coolant tank.
- *12 Value for turret magazine plus tool stocker
- *13 Value for turret magazine
CNC model | CNC-D00《S300Xd2/S500Xd2/S700Xd2》 | |
---|---|---|
Control axes | 5 axes (X, Y, Z, 2 additional axes) | |
Simultaneously controlled axes | Positioning | 5 axes (X, Y, Z, 2 additional axes) |
Interpolation |
Linear : 4 axes (X, Y, Z, 1 additional axes) Circular : 2 axes Helical/Conical : 3 axes (X, Y, Z) |
|
Least input increment | 0.001mm、0.0001inch、0.001 deg. | |
Max.programmable dimension | ±999999.999mm、±99999.9999inch | |
Display | 15-inch color LCD touch display | |
Memory capacity | 500 Mbytes, 3 Gbytes (optional) (Total capacity of program and data bank) |
|
External communication | USB memory interface, Ethernet, RS232C (optional) | |
No.of registrable programs | 4,000 (Total capacity of program and data bank) | |
Program format | NC language, conversation (changed by parameter) Conversation from conversation program to NC language program available * Only NC language available on the S700Xd2-100T. Conversation language not available |
CNC model | CNC-D00v(DB)《S300Xd2-5AX/S500Xd2-5AX/S700Xd2-5AX》 | |
---|---|---|
Control axes | 5 axes (X, Y, Z, 2 additional axes) | |
Simultaneously controlled axes | Positioning | 5 axes (X, Y, Z, 2 additional axes) |
Interpolation |
Linear : 5 axes (X, Y, Z, 2 additional axes) Circular : 2 axes Helical/Conical: 4 axes (3 linear axes + 1 additional axis, 2 linear axes + 2 additional axes) |
|
Least input increment | 0.0001 mm, 0.00001 inch, 0.0001 deg. | |
Max.programmable dimension | ±999999.9999 mm, ±99999.99999 inch | |
Display | 15-inch color LCD touch display | |
Memory capacity | 3GB (Total capacity of program and data bank) | |
External communication | USB memory interface, Ethernet, RS232C (optional) | |
No.of registrable programs | 4,000 (Total capacity of program and data bank) | |
Program format | NC language * Conversation language not available |
- * Number of "control axes" and/or "simultaneously controlled axes" are the maximum number of axes, which will differ depending on the destination country and the machine specifications.
- * Ethernet is a trademark or registered trademark of XEROX in the United States.
Operation | Dry run Machine lock Program restart Rapid traverse override Cutting feed override Background editing Screen shot Operation level External input signal key Shortcut keys
|
|
---|---|---|
Programming | Absolute / Incremental Inch / Metric Coordinate system setting Corner C / Corner R Rotational transformation Synchronized tap Subprogram Graphic display |
|
Measurement | Automatic workpiece measurement *1 Tool length measurement |
|
High speed and high accuracy | Machining parameter adjustment High-accuracy mode AIII High-accuracy mode BI (look-ahead 160 blocks) Backlash compensation Tool center point control *3 *4 (Look-ahead 1,000 blocks)
|
|
Monitoring | Machining load monitoring ATC monitoring Overload prediction Waveform display / Waveform output to memory card Heat expansion compensation system ll (X, Y, and Z axes) Production performance display Tool life / Spare tool Chip detection function |
|
Maintenance | Tap return function Status log Alarm log Operation log Maintenance notice Motor insulation resistance measurement Tool washing filter with filter clogging detection Battery-free encoder Breake load test |
|
Automatic / Network | Computer remote OPC UA Auto notification Built-in PLC (LD/ST/FBD)
|
|
Energy saving | Automatic power off Standby mode Automatic coolant off Automatic work light off Chip shower off delay Chip shower energy savings operation Energy savings mode |
|
Support apps | Adjust machine parameters ATC tool Tool life Waveform display Production performance Power consumption Recovery support Inspection PLC No warmup support function |
|
Accessories | File viewer Notebook Calculator Register shortcut Display off |
|
Functions limited to NC language | Menu programming Local coordinate system Expanded workpiece coordinate system One-way positioning Inverse time feed Programmable data input Tool length compensation Cutter compensation Scaling Mirror image External sub program call Macro Tape operation / FTP load operation Multiple skip function
|
|
Functions limited to conversation language *6 | Operation program Schedule program Automatic tool selection Automatic cutting condition setting Automatic tool length compensation setting Automatic cutter compensation setting Automatic calculation of unknown number input Machining order control |
- *1 Measuring instrument needs to be prepared by users.
- *2 When the submicron command is used, changing to the conversation program is disabled.
- *3 There are restrictions on the axis configuration.
- *4 Available only on the S300/S500/S700Xd2-5AX.
- *5 Standard on the S300/S500/S700Xd2-5AX.
- *6 Conversation language not available on the S300/S500/S700Xd2-5AX.
Example
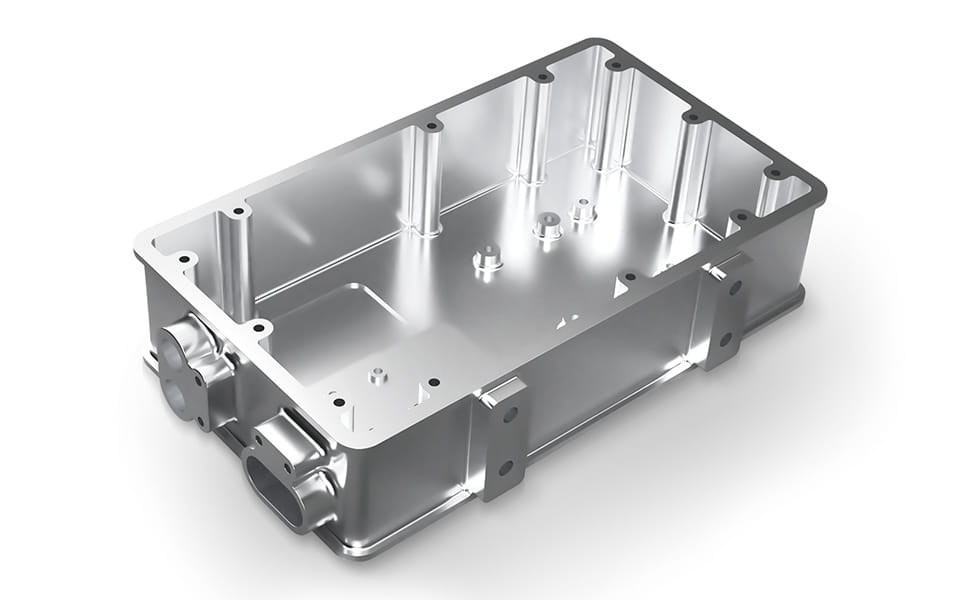
Aluminum Alloy
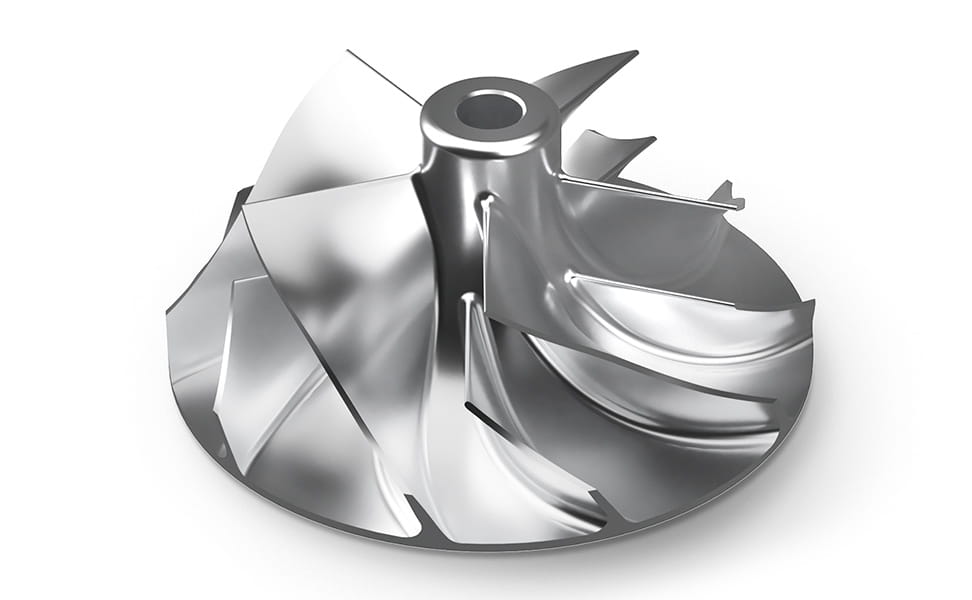
Aluminum Alloy
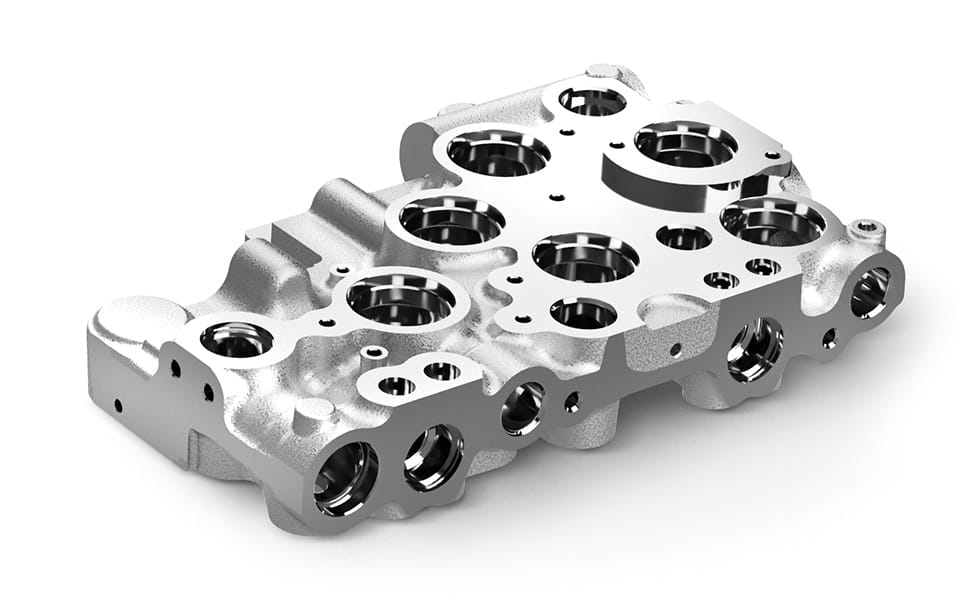
Aluminum alloy
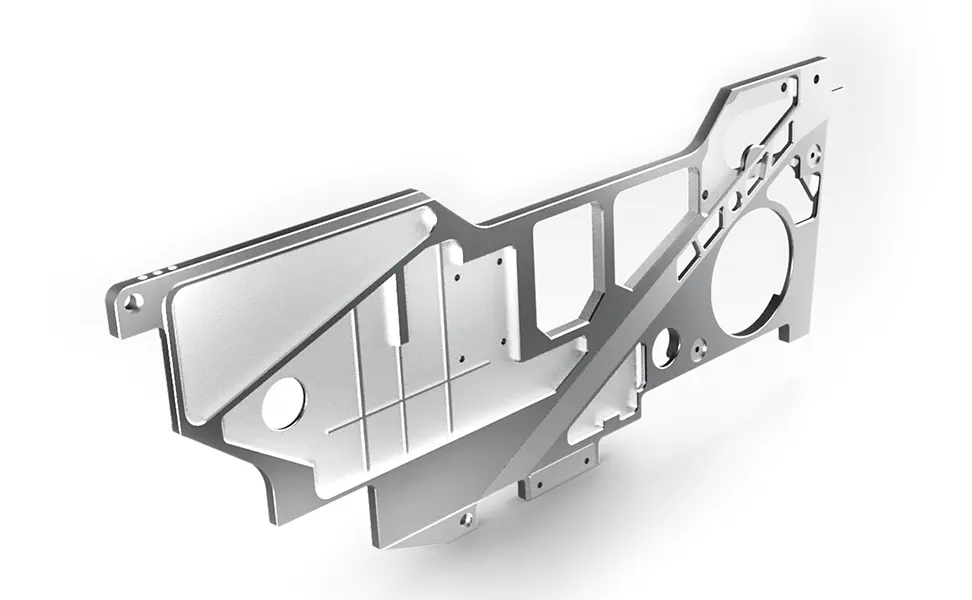
Aluminum Alloy
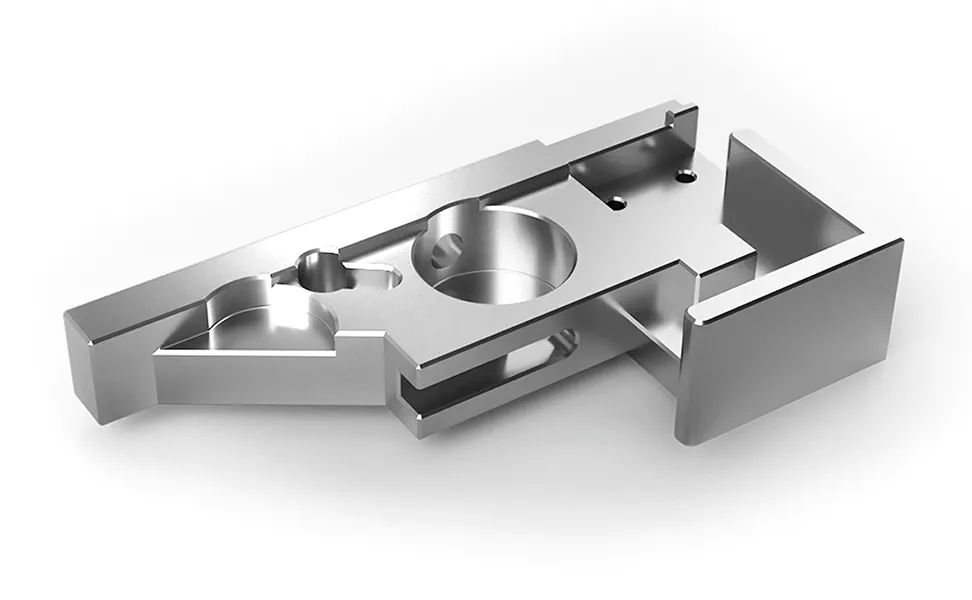
Stainless steel
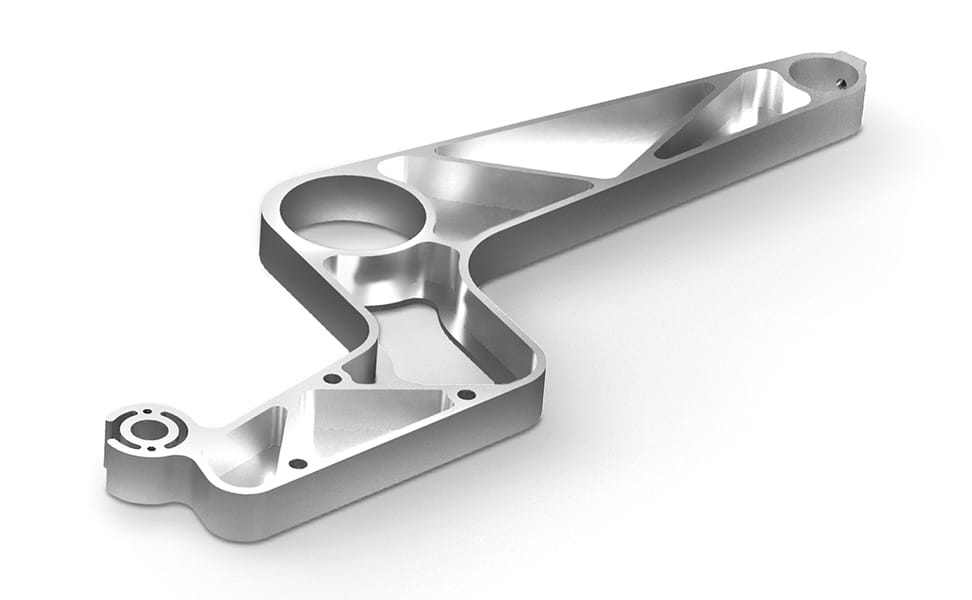
Aluminum alloy